Decarbonizing Ethylene and Propylene Production
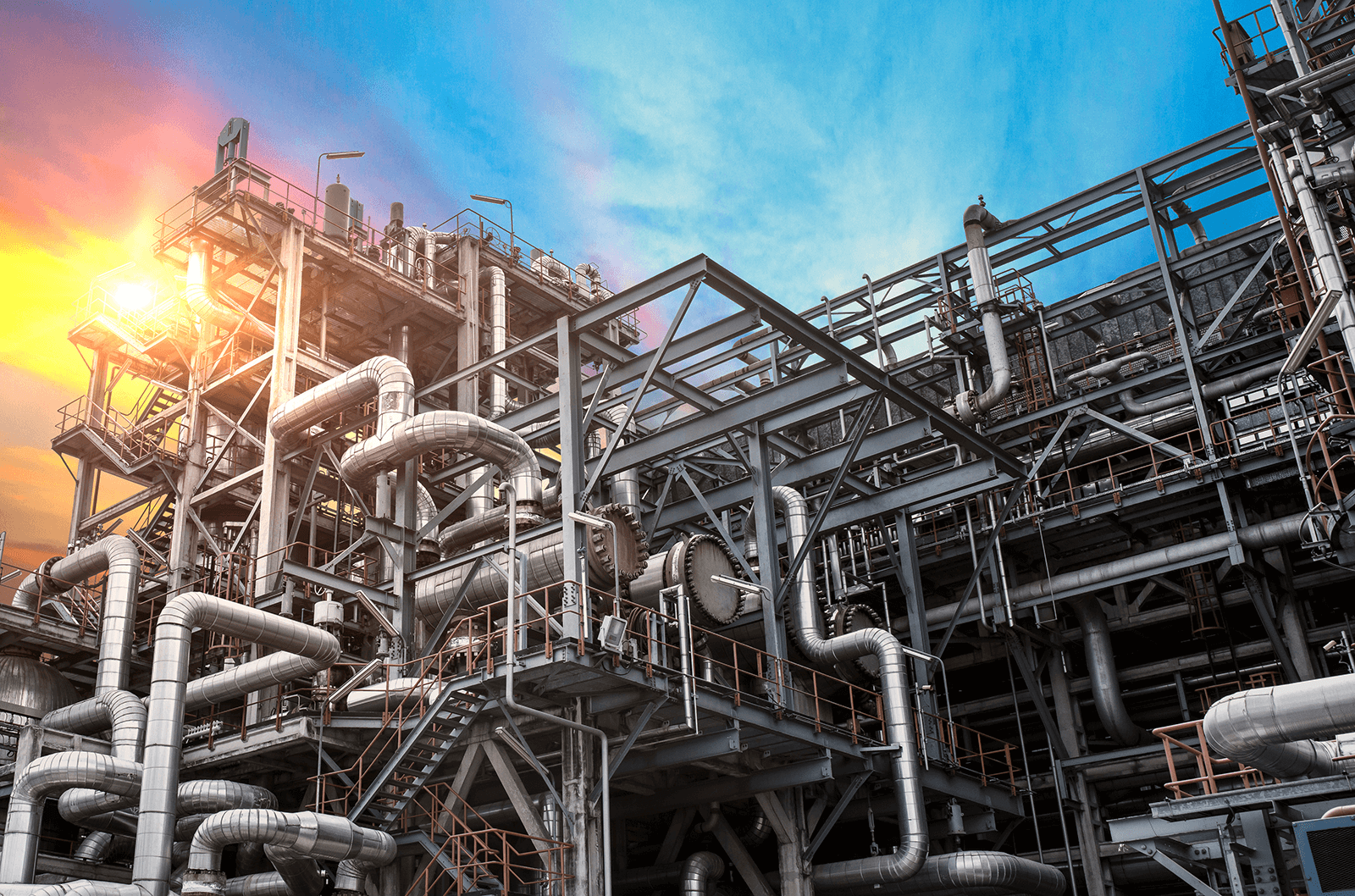
Chemistry plays a big role in our everyday lives. In one form or another, manufactured chemicals extend into cleaning, communication, transportation, medical supplies, pharmaceuticals and equipment. Even new innovations within energy and energy-efficient technology, such as plastic solar panels stem from this industry. Recently, the business of chemistry reached €5.2 trillion, which is ~7% of the global GDP (Mulder, 2019).
While providing exceptionally useful products, it is no surprise the industry is subject to the heaviest regulations. And decarbonising production will also be a landscape the industry must navigate. Even so, the chemical industry has the greatest potential for increasing sustainability within global manufacturing, as many production processes are energy intensive.
In fact, the chemical industry accounts for 28% of the total industrial energy demands in the United States alone (Leow et al., 2020). Much of this demand comes from burning fossil fuels to reach the heat for steam-cracking furnaces. These furnaces are typically employed to create two light hydrocarbons, ethylene and propylene. Together, the two gases make up the base chemical component for 60% of all commercial organic chemicals (Gholami et al., 2021).
Why going green isn't an option for the chemistry industry
The need for chemical products is expected to accelerate as global manufacturing transitions towards renewable energy, including technologies dependent on, for example, plastics. It may be logical to conclude that the chemical industry seeks a means to decarbonise its production processes. Failure to do so would render the decarbonisation efforts made elsewhere by other industries and governments pointless.
Olefins can prove a solution to this goal. These light hydrocarbon gases are produced at a greater level than any other class of chemicals. Of those olefins, ethylene and propylene make up the largest proportion, and steam cracking is one of the most common ways of producing them. So, when chemical producers seek a more sustainable production process, steam cracking could be a smart place to start.
The carbon facts on steam cracking
While steam cracking is the most mature and cheapest chemical production process, it’s also the most energy intensive and environmentally damaging. Steam cracking accounts for more than 300 million tons of CO2 emissions yearly (Amghizar et al., 2020). That is nearly 1.2% of global yearly CO2 emissions that can be addressed by the chemistry industry alone (Tiseo, 2024).
This means that finding ways to reduce CO2 emissions through alternative energy sources would mitigate the environmental impact of steam cracking.
How are ethylene and propylene produced?
Olefins like ethylene and propylene are produced by breaking down natural gas liquids, known as feedstocks, into their constituent parts. There are many different processes by which olefins are produced from natural gases (Phung et al., 2021). Currently, the most established and widely used processes are energy-intensive and emit generous amounts of greenhouse gasses to be sustainable, they include (Ren et al., 2006):
- olefin catalytic cracking
- propane dehydrogenation and oxidative dehydrogenation
- metathesis propylene production
- steam-enhanced catalytic cracking
- steam cracking
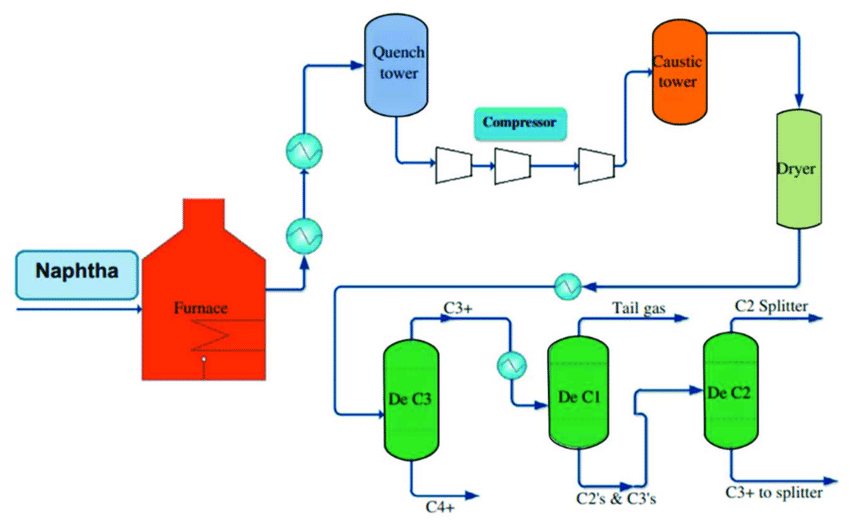
Steam cracking is the most widely adopted process for producing olefins from natural gas liquids. This is primarily because it’s more profitable for chemical producers. For example, steam cracking has the lowest total production cost (TPC) of any current olefin-producing process (Gholami et al., 2021).
Heat characteristics of steam cracking
Steam cracking is the process of feeding natural gas and steam inside an exceptionally hot furnace under pressure without the presence of oxygen. Depending on the natural gas being used and the desired olefin to produce, furnaces must first heat up to 800-850 °C. Then there is a rapid drop to 400-500 °C to prevent downstream reactions after the initial splitting (Gholami et al., 2021).
The reaction time needed to split natural gas into olefins like ethylene and propylene is around 0.01-0.02 seconds. In other words, the temperature must drop 300-400 °C faster than the blink of an eye (Amghizar et al., 2020). This “quick cooling” can be particularly challenging because the process creates an endothermic reaction, whereby the chemicals splitting apart in the furnace absorb the surrounding energy and become intensely hot.
To achieve the rapid drop in temperature, the separated gas mixture is forced into a series of cooling tubes called transfer line exchanges (TLE). From the furnace, the now separate chemicals transition through several stages of distillation, chemical treatment, and separations to lastly reach the desired gaseous and liquid olefins.
A green solution for ethylene and propylene production
Several “green” processes for lessening olefin production's environmental impact have been developed recently. For example, methanol-to-olefins (MTO), ethanol-to-propylene (ETP), and bioethanol dehydration, dimerization and metathesis (Phung et al., 2021). While the horizon is promising, these processes are immature, need greater industry adoption and require further optimization to maintain profitability before they can serve as a decarbonizing alternative. Industry experts must seek ready innovations that are deployable today, and steam cracking is just one established process suitable for existing green solutions (Amghizar et al., 2020).
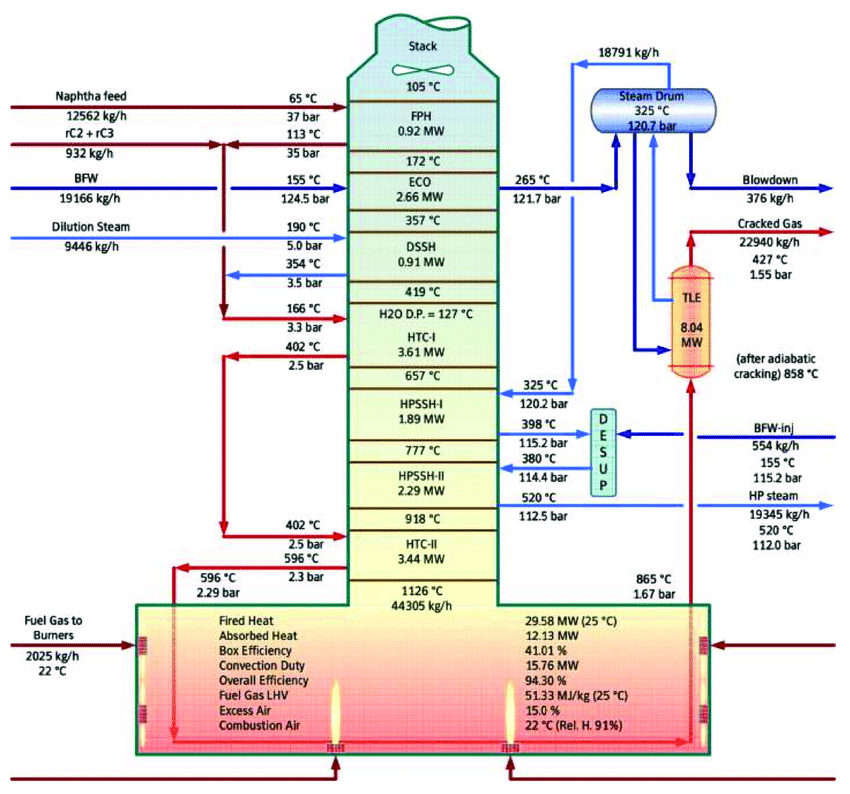
CO2 output of steam cracking can be lowered by:
- substituting the energy derived from fossil fuels to heat furnaces, e.g. with electric furnaces
- improving heat transfer
- reducin coke formation on the furnace walls
The first reflex would be to think of replacing natural gas with green hydrogen, but apart from the cost of availability questions, the issue of more volume needed with hydrogen needs to be considered. Thus, retrofitting furnaces need to be researched.
Changing the furnace to an electric furnace also brings some changes with it, but naturally is more cost-efficient than hydrogen. In a first of a kind installation, BASF, SABIC and Linde installed two e-furnaces to steamcrack gases. One uses electrical current directly to heat up the pipes, steam flows through, one uses resistance heating elements and their radiative heat wrapped around the pipes (BASF.com, 2024). The systems together have 6 MW, so the tests run on industrial but not full-scale.
As this is a first of its kind project, supported with nearly €15 million by the German government, one might also think about testing the retrofit of traditional furnaces for hot air driven processes, which can be flexible through Kraftblock. What in theory is possible with temperatures reaching up to 1150 °C would need to be tested regarding the integration of hot air instead of burning gas, which has different volume flows and energy density.
Capture and redistribute heat loss from stream cracking
With every rapid drop in temperature needed to split natural gas into olefins like ethylene and propylene, excess heat is lost and could be recycled. Some heat is effectively recycled via water-cooled TLE tubes, which can be reused via steam at the start. However, much of the excess heat from the burning of the furnace is released via flue gases. A lot of waste heat recovery already is done in steam cracking. When there are losses, the capture and reuse of hot flue gas could improve the overall efficiency.
References
Amghizar, I., Dedeyne, J. N., Brown, D. J., Marin, G. B., & Van Geem, K. M. (2020). Sustainable innovations in steam cracking: CO 2 neutral olefin production. Reaction Chemistry & Engineering, 5(2), 239-257.
basf.com (2024): BASF, SABIC, and Linde celebrate the start-up of the world's first large-scale electrically heated steam cracking furnace. Online: https://www.basf.com/global/en/media/news-releases/2024/04/p-24-177.html
Gholami, Z., Gholami, F., Tišler, Z., & Vakili, M. (2021). A review on the production of light olefins using steam cracking of hydrocarbons. Energies, 14(23), 8190.
Leow, W. R., Lum, Y., Ozden, A., Wang, Y., Nam, D. H., Chen, B., ... & Sargent, E. H. (2020). Chloride-mediated selective electrosynthesis of ethylene and propylene oxides at high current density. Science, 368(6496), 1228-1233.
Mulder, M. (2019). Chemical Industry Contributes $5.7 Trillion to Global GDP and Supports 120 Million Jobs, New Report Shows. The European Chemical Industry Council. https://cefic.org/media-corner/newsroom/chemical-industry-contributes-5-7-trillion-to-global-gdp-and-supports-120-million-jobs-new-report-shows/
Phung, T. K., Pham, T. L. M., Vu, K. B., & Busca, G. (2021). (Bio) Propylene production processes: A critical review. Journal of Environmental Chemical Engineering, 9(4), 105673.
Ren, T., Patel, M., & Blok, K. (2006). Olefins from conventional and heavy feedstocks: Energy use in steam cracking and alternative processes. Energy, 31(4), 425-451.
Tiseo, I. (2024). Annual Global emissions of carbon dioxide 1940-2023. Statista. https://www.statista.com/statistics/276629/global-co2-emissions/.