Whitepaper: Comparison of Technologies to decarbonize Process Heat in Industries
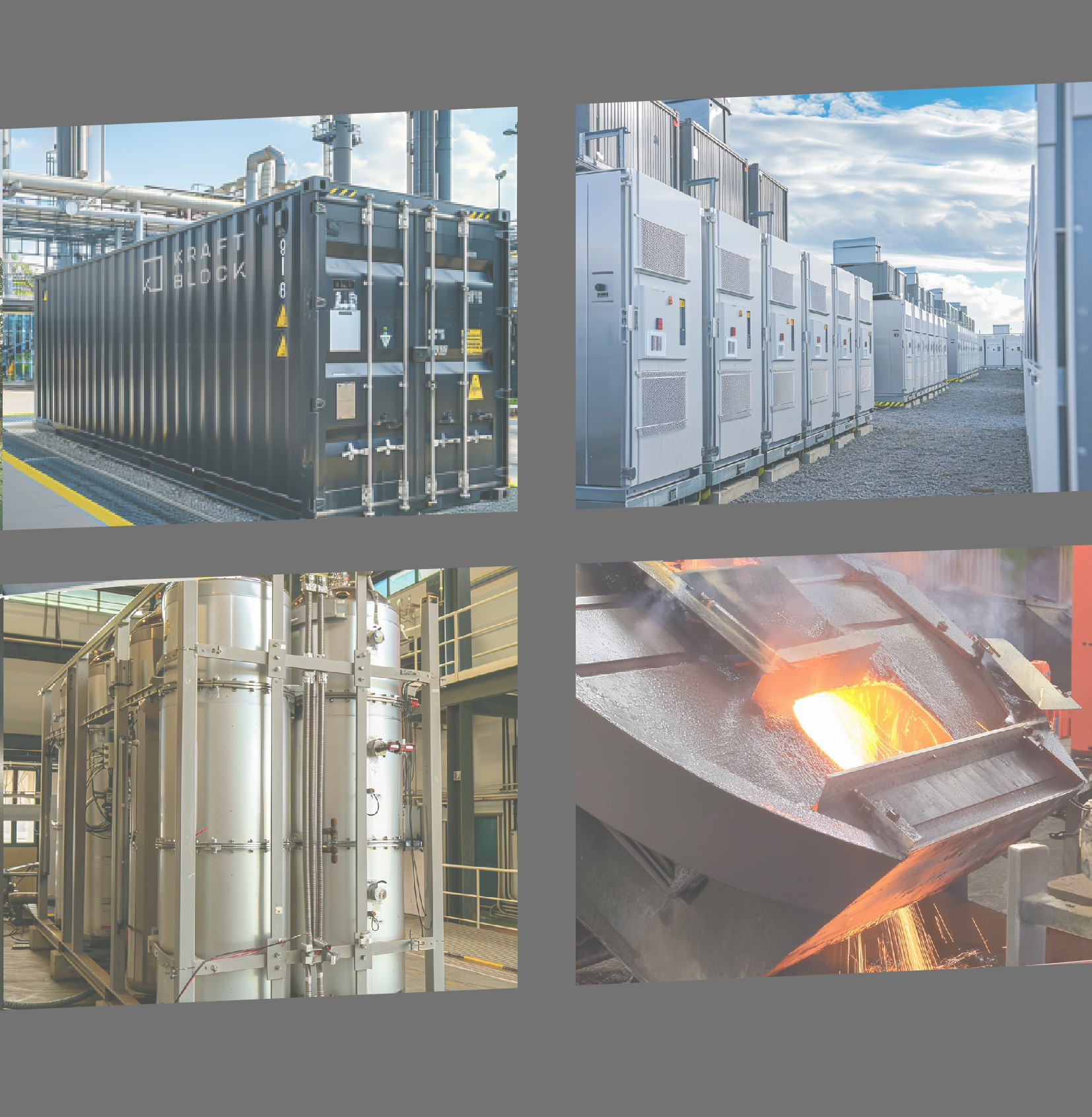
This article covers the executive summary of Kraftblock's whitepaper. The whitepaper can be requested by sending an email to cedric@kraftblock.com with the subject "Whitepaper".
Comparison of hydrogen, battery storage, direct electrification and thermal energy storages
One of the most important levers on the path to net zero is replacing fossil fuels in industry. Depending on the sector, process heat accounts for up to 70% of industrial energy consumption and more than a quarter of global emissions. This is equivalent to the emissions of China and the EU. This major lever for reducing emissions has been overlooked for a long time and is now coming to the forefront as decarbonization targets are missed.
How to replace fossil fuels, especially in heavy industry, seems to be a difficult question as demonstration projects are still rare. Despite many years of planning for green hydrogen projects, there is basically no green hydrogen in use. With more and more cheap, renewable electricity and exploding solar and wind generation capacity projects, electrification solutions are in focus today. In addition, technologies such as thermal energy storage and batteries have matured to the point of commercial use in industries. While a specific project has many more variables than an overarching comparison can integrate, there is now enough knowledge to provide guidance and explain what different technologies can achieve in the decarbonization of industries.
For this comparison, we included technologies that are often discussed for decarbonizing industries. For direct electrification, these are induction furnaces and electric boilers among others. For flexible electrification, thermal energy storage plus power-to-heat and battery storage plus power-to-heat were analyzed. Less scalable but often discussed are bioenergy fuels and green H2. It should be noted that for very low temperature process heat, heat pumps are a viable and cost-effective solution, but are limited to about 150 °C – 170 °C. As CCS is not yet a commercially viable solution, it was not considered, but there is data in the white paper that includes partial comparisons.
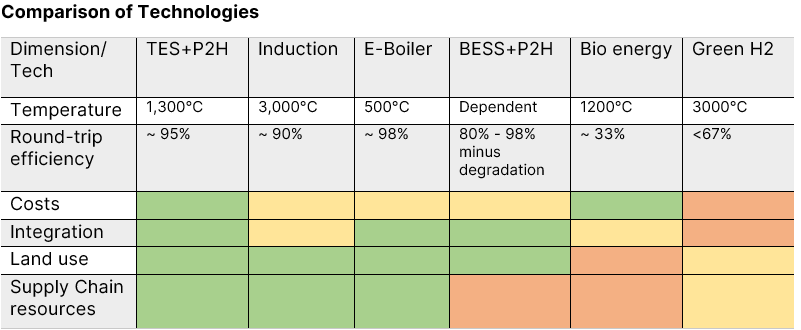
The determination of the best solution for decarbonizing process heat is, of course, highly dependent on costs: These depend strongly on OPEX and less on CAPEX, as the examples from the analyzed technologies and fossil technologies show. This means that the price of electricity, which is the primary fuel for all technologies except bioenergy, is the most important indicator of technology cost. And it also means that the flexibility in electricity procurement through storage has a significant advantage in OPEX costs, with cost savings of up to about 15% compared to direct electrification (see white paper for details).
Batteries, which have a high payback for grid stabilization tasks, have higher CAPEX costs than thermal energy storage that can use waste products for storage material, as in the case of Kraftblock. Due to degradation and replacement after about ten years , twice as many batteries are needed in a case thermal energy storage can be used and live twice as much cycles. E-boiler with batteries might however be a good use case for middle-temperature applications under 1 MW. Induction furnaces, although limited to conductive material, will have a crucial role for energy intense processes over 1000 °C.
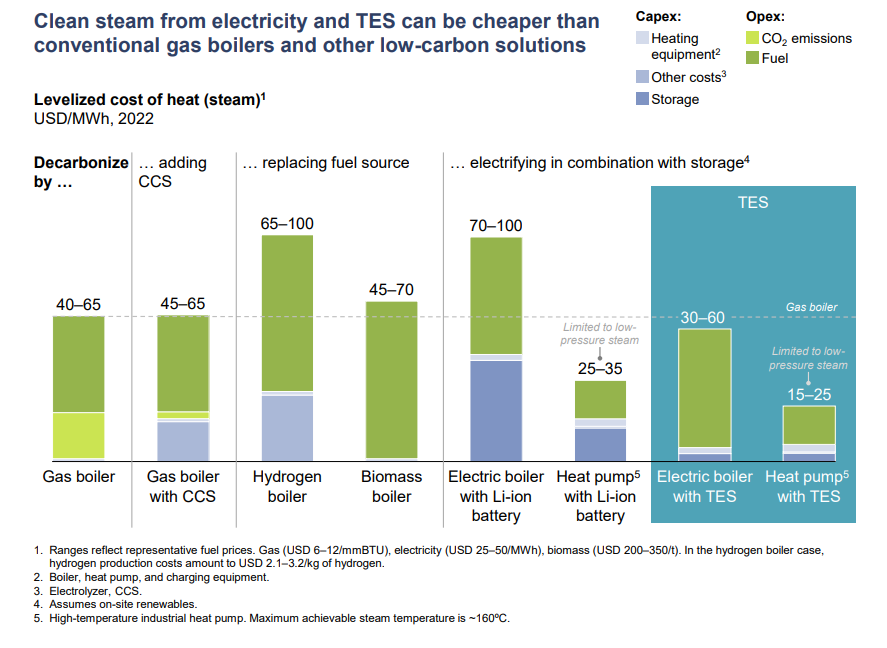
Key resources and the supply chain are the most important factors in cost development. Electrification technologies such as resistance heaters for power-to-heat, e-boilers or induction furnaces, while using a lot of metal, mostly use non-critical resources with a established supply chain. For commercial lithium-ion batteries, lithium is a critical resource, and while prices have fallen sharply recently, there is still a gap between supply and demand for mining for future needs.
Hydrogen does not yet have a supply chain in terms of production and distribution. Only 1% of the hydrogen used in the EU is green, and production capacity lags far behind EU targets. Bioenergy is dependent on large areas of land, competes with food sources and will become increasingly critical as droughts increase. The limited scalability of bioenergy and hydrogen makes neither technology a viable use case for most industries.
A comparison of the often discussed technologies shows that flexible solutions with scalable green energy sources have a huge advantage, being able to use more electricity from negative-prized hours and stabilizing the grid, while inflexible solutions suffer from higher OPEX. The combination of electrification and inexpensive thermal energy storage is the best use case for most industries, from food, pulp and paper to ceramics drying, zinc heating oreven high temperature processes in chemicals and steel. This is getting more clear on the detailed discussion of the aspects in this comparison.
If you are interested to learn these details, reach out to us and write an e-mail at cedric@kraftblock.com with the subject 'Whitepaper' to receive the 20-page document.