Upcycling Energy in Urban Mining
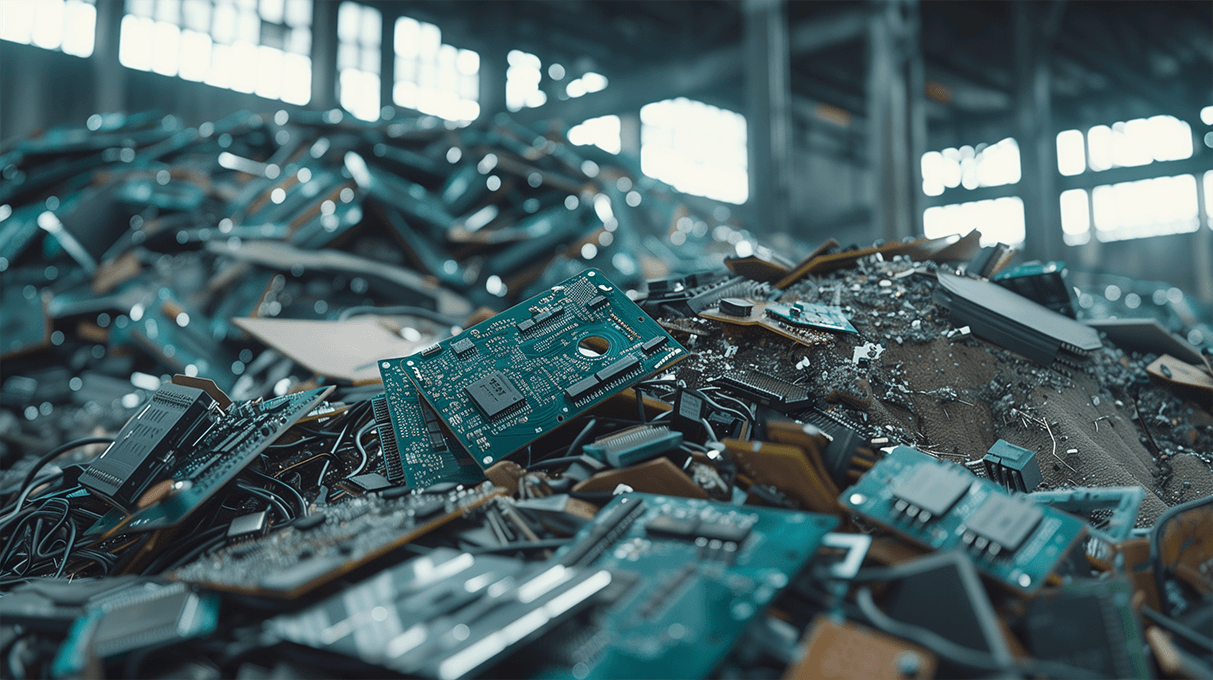
The digital revolution has led to a massiveuptick in physical technology, including an explosion in electronic waste(e-waste). While the technology may grow old and outdated, individual components often retain their value long after a smartphone has gone dark, making a case for recycling.
E-waste is the fastest growing type of refuse in the world (World Economic Forum, 2019). It’s also one of the most toxic to both individual and environmental health. But e-waste is also a massive economic opportunity. It’s estimated that the total value of raw materials - like plastics, Cu, Fe, Al, Co, Ni, Sn, Pb, Zn, and precious metals gold and silver - that can be recycled from e-waste is over €54 billion per year (Liu etal., 2023).
Taking old, outdated electronics and recycling them is called ‘urban mining.’ It offers a literal and proverbial gold mine for countries and industries willing to invest in making the process more efficient and environmentally friendly. And of course there is heat involved in recovering the metals from the waste, which needs decarbonization.
Opportunities and challenges in urban mining
Recycling e-waste is crucial to combating the scarcity of rare earth minerals and precious metals and contributing to a circular economy including the energy economy. For example, recycling 1 million laptops saves the energy equivalent to that used by 3,600 homes used in the US each year (EPA, 2015). Meanwhile, it’s estimated that around 50 million tonnes of e-waste are produced each year (Iberdrola, 2024). Despite laws like the Basel Convention (1989) aiming to restrict the movement of e-waste, there's a thriving illegal industry transporting it from developed to developing nations. This poses significant issues: developing nations often lack safe disposal methods, leading to hazardous working conditions and environmental damage. Meanwhile, developed nations lose out on potential recycling revenue.
Urban mining also faces challenges in finding efficient, eco-friendly methods. Experimental techniques like supercritical fluid, molten salt, and bioleachingshow promise but need further development to balance cost-effectiveness withvalue (Liu et al., 2023).
Processes like hydrometallurgy and pyrometallurgy have proven to be extremely effective in recovering precious metals from e-waste. The one caveat is that they currently produce higherlevels of GHG emissions that tilt the environmental balance out of whack. Thus, one should revisit existing processes and review new technology for greener urban mining.
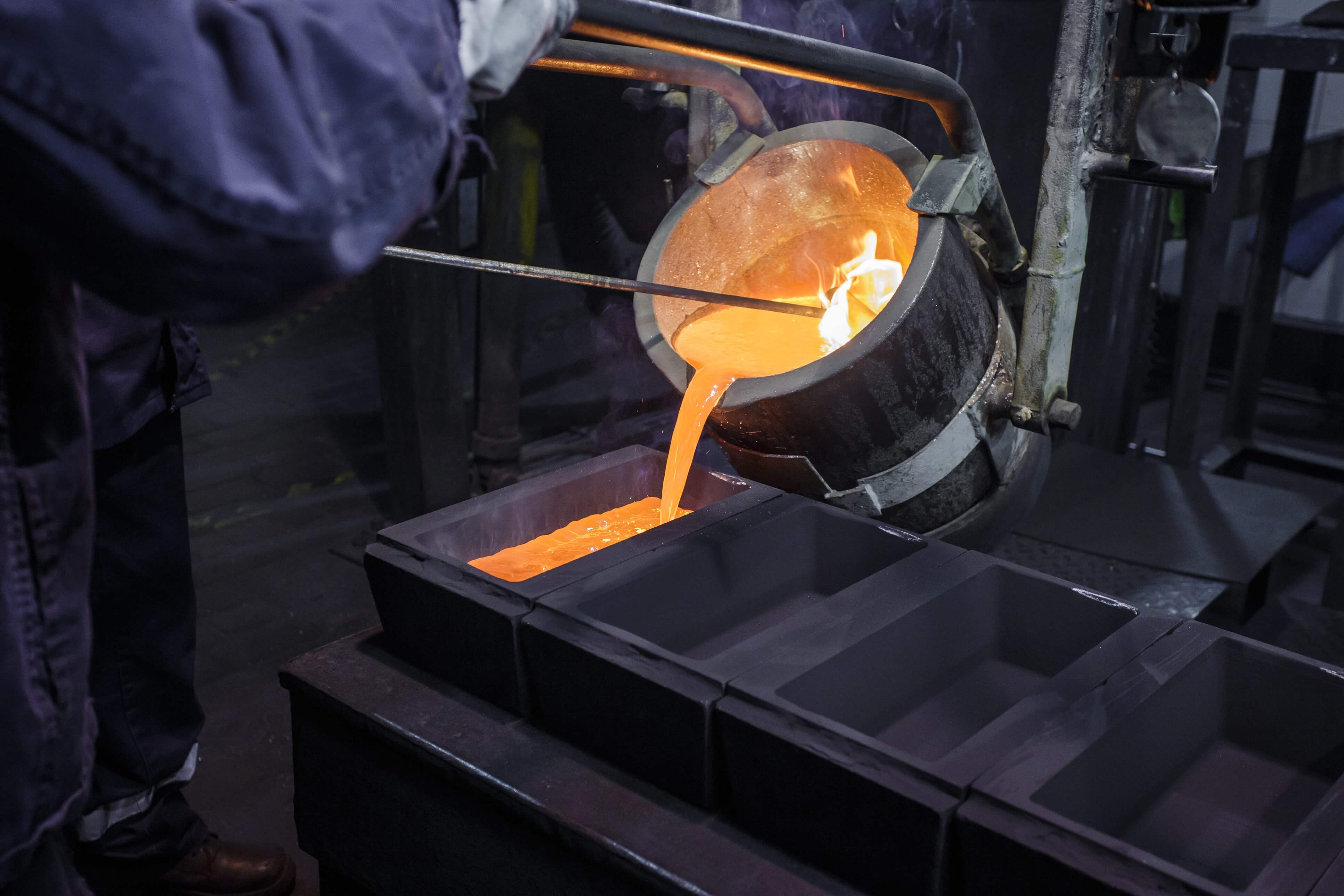
Replacing fossils and using waste heat to save energy and reduceGHG emissions
Pyrometallurgy is one of the most widely used processes for treating e-waste. Compared to newer experimental processes, the upside of this process is its relative simplicity and effectiveness. Also, there is no need for sorting and size reduction in pyrometallurgy as the process begins by shredding the e-waste into smaller particles (Castro &Bassin, 2022). However, extracting precious metals requires high-temperature process heat, which is also tied to high CO2 emissions and energy consumption. If process heat for pyrometallurgy could be green and waste heat could be upcycled, this would improve energy efficiency and reduce GHG emissions.
The heat needed to turn e-waste into profitable precious metals
In the pyrometallurgical process, e-waste is first run through shredders or grinders, which break the metal by-products into smaller particles. The next step is to smelt the shredded mass using either flash or batch furnaces. This process results in separated metals, leftover slag, and flue gasses (Castro & Bassin, 2022). From here, pyrometallurgy becomes a more varied process depending on the facility and the primary metal makeup of the separated metals (Harvey et al., 2022):
- Primary iron loads can be further separated by oxygen and electrical arc furnaces
- Copper and lead loads can be separated by smelting furnaces
- Aluminium loads can be separatedby tilting or stationary melting furnaces
The primary benefit of all these pyrometallurgy methods is that they efficiently separate precious metals ataround 99.99% (Liu et al., 2023).
A consistent challenge to the economic and environmental efficiency of pyrometallurgy is the need for high heat. The process of pyrometallurgy, depending on the exact method, requires sustained heat between 400°C and 1200°C (Kiehbadroudinezhad, 2023). For example, copper-smelting, which introduces sulfides to facilitate separation, requires 1200°C, while lead-smelting using blast and imperial smelting furnaces requires a lower temperature between 400°C and 800°C (Harvey et al., 2022). This heat is generated mostly by fossil fuels, making the positive effect of recycling used materials less environmentally friendly by emitting large amounts of GHG and CO2. Some of the furnaces can be operated with hot air from Kraftblock’s Net-zero heat system, using renewable energy. The reuse of the hot flue gas alone to preheat scrap or furnaces may lead to a significant reduction of fossil fuels needed.
Copper-smelting e-waste, an example process of pyrometallurgy
One of the most common forms of pyrometallurgy in urban mining is copper-smelting. This is because of the high copper content in circuit boards, a primary component in almost all e-waste. After the e-waste has been mechanically separated and shredded, the high copper shredded mass is fed into a smelting furnace alongside mined copper concentrates (Rath et al.,2022).
This initial process separates copper alloy and other precious metals from iron, lead, nickel and other less valuable materials. The copper alloy mass is then processed using electrorefining and chemical leaching to separate the copper from other precious metals like gold,silver, and platinum.
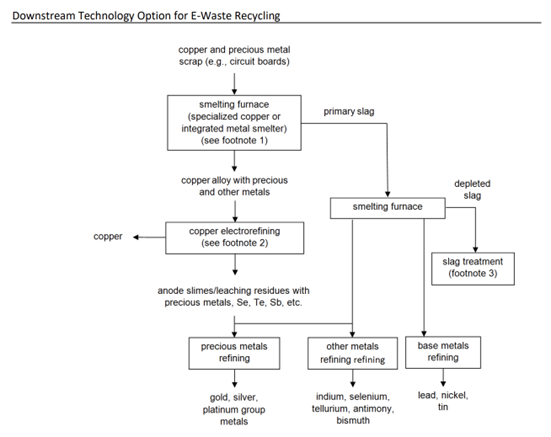
Meanwhile, the metal slag from the first smelting furnace is smelted again using techniques to further separate the iron, lead, nickel, and other materials (GIZ E-Waste Programme Ghana, 2019).This process uses high heat at multiple stages, making heat retention a valuable component in making pyrometallurgy more economically and environmentally efficient.
The need for high temperatures in recycling e-waste
The high level of consistent heat required for pyrometallurgy in recycling e-waste is the primary obstacle to making the technique the best industry option for urban mining. So, capturing heat from smelting furnaces, especially in batch processes, and storing it until the next work cycle could dramatically lower GHG emissions and save recycling plants from burning excess fossil fuels.
Other use cases of this stored heat include industrial local heating and grid heating (Hajlasz et al., 2023). As the demand for precious metals increases, finding means of creating and recycling materials on the same site can raise potential revenues and lower GHG emissions.As we accelerate into a new epoch of technology, the need to recycle the last generation’s technology will be important to fuel further growth. This should include experimenting with new forms of e-waste recycling and perfecting older, more mature forms like pyrometallurgy.
References
Castro, F. D., &Bassin, J. P. (2022). Electronic waste: Environmental risks and opportunities.In Hazardous Waste Management (pp.421-458). Elsevier. https://doi.org/10.1016/B978-0-12-824344-2.00002-1
GIZ E-WasteProgramme Ghana. (2019). Downstream Technology Option for E-waste Recycling.https://www.giz.de/en/downloads/giz2019-en-business-option-e-waste-recycling.pdf
Global Atmospheric CO2 Concentration,World. https://ourworldindata.org/explorers/climate-change?time=earliest..1990-08-15&facet=none&country=~OWID_WRL&hideControls=true&Metric=CO%E2%82%82+concentrations&Long-run+series=falsehttps://ourworldindata.org/explorers/climate-change?time=earliest..1990-08-15&facet=none&country=~OWID_WRL&hideControls=true&Metric=CO%E2%82%82+concentrations&Long-run+series=false (Date of last access March 27th,, 2024).
Hajlasz, M., Helmcke, S., Liebach, F., Schleyer, T.,& Somers, K. (2023, November 30). Unlocking the potential of waste heat recovery |McKinsey. Www.mckinsey.com; McKinsey Sustainability. https://www.mckinsey.com/capabilities/sustainability/our-insights/waste-not-unlocking-the-potential-of-waste-heat-recovery
Harvey,J. P., Khalil, M., & Chaouki, J. (2022). Pyrometallurgical processes forrecycling waste electrical and electronic equipment. Electronic Waste:Recycling and Reprocessing for a Sustainable Future, 135-164.
Iberdrola. (2024). What istechnological waste? Technological pollution, a 21st century problem.https://www.iberdrola.com/sustainability/what-is-e-waste
Kiehbadroudinezhad,M., Merabet, A., & Hosseinzadeh-Bandbafha, H. (2023). Electronic Waste to Energy, Technologies, Economics, andChallenges: A Renewable or Non-Renewable Path?. https://doi.org/10.1016/B978-0-323-93940-9.00126-2
Liu,K., Tan, Q., Yu, J., & Wang, M. (2023). A global perspective on e-waste recycling. Circular Economy, 2(1), 100028.https://doi.org/10.1016/j.cec.2023.100028
Rath, S. S., Nayak, P.,Mukherjee, P. S., Chaudhury, G. R., & Mishra, B. K. (2012). Treatment ofelectronic waste to recover metal values using thermal plasma coupled with acidleaching–A response surface modeling approach. Waste management, 32(3),575-583.
U.S. EnvironmentalProtection Agency. "Wastes - Resource Conservation - Common Wastes &Materials - eCycling." Web Accessed April 11, 2015.
World Economic Forum (2019,January). A New Circular VIsion forElectronics: Time for a Global Reboot. https://www3.weforum.org/docs/WEF_A_New_Circular_Vision_for_Electronics.pdf