Carbon-neutral solutions for the quietly growing impact of Acrylic Acid
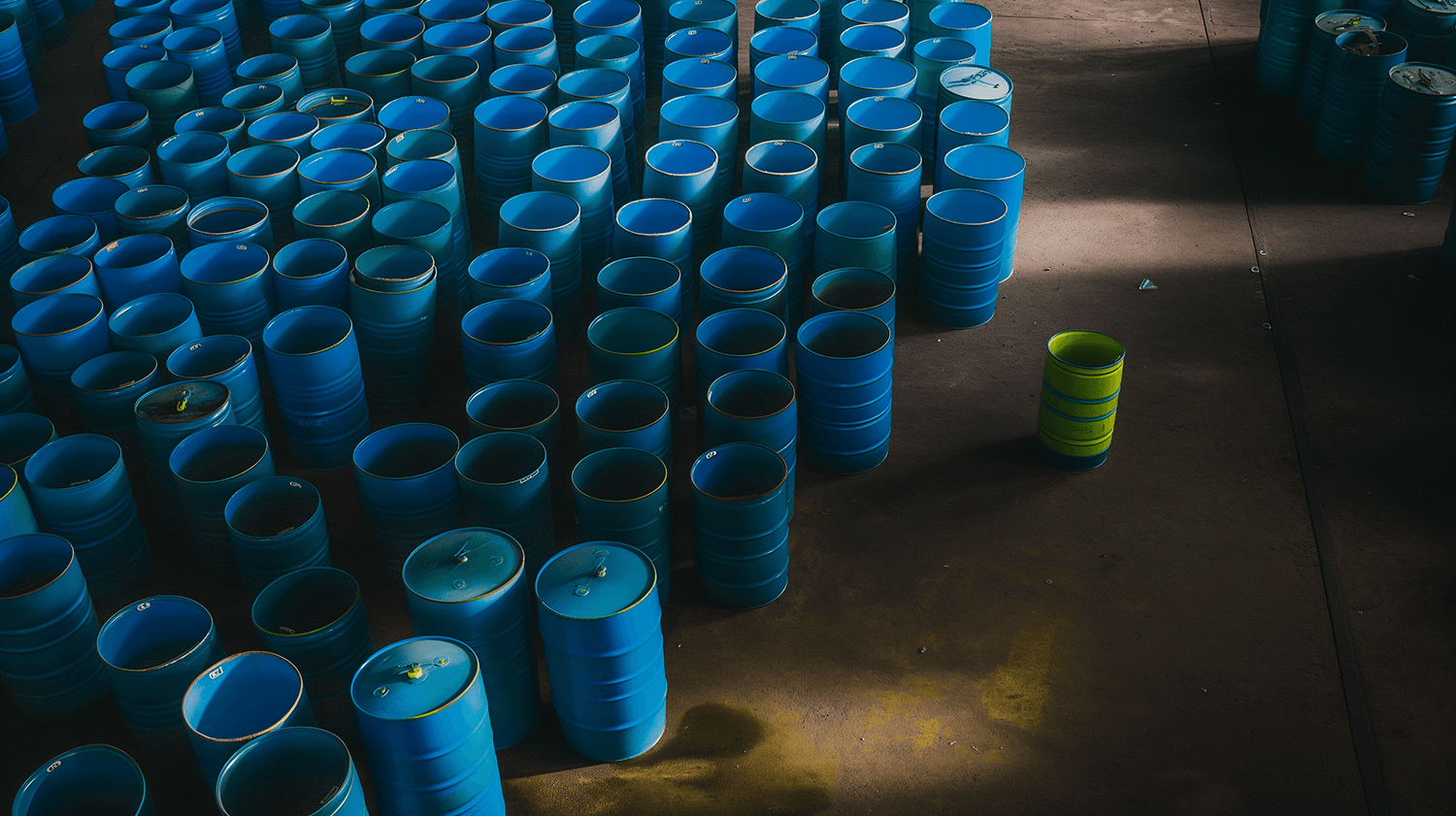
Products from the petrochemical industry surround us daily, from the clothes we wear to the floors we walk on. Acrylic acid is one product quietly forming the basis of diapers, paints, adhesives, and coatings, among other things, while also serving as a crucial ingredient for producing plastics, resins, and rubbers (BASF, 2012). Globally, the product is so widespread that it has acquired indispensable status.
In 2020, the global acrylic acid market was valued at $12.0 billion and is projected to reach $19.2 billion by 2030. Over the next decade, the CAGR for the acrylic acid market will steadily increase between 3% and 4.8% (Allied Market Research, 2022; S&P Global, 2023). While mainland China and Europe are some of the largest consumers, the USA, Japan, and South Korea are not far behind.
Given the widespread global usage of acrylic acid, environmental attention is intensifying, particularly regarding the high demand for fossil fuels in the production process. Though the reliance on fossil fuels for acrylic acid production poses challenges, innovations offer sustainable alternatives. Many provide realistic and economically viable options for reducing environmental footprints. Two approaches could significantly reduce the carbon footprint of acrylic acid production. The first involves optimizing how the production processes are heated, and the second focuses on the sourcing and processing raw materials. Both are intricately linked.
What are conventional and bio-based Acrylic Acid processes?
Crude acrylic acid (CAA) is typically made from the oxidation of the hydrocarbon propylene. About half is turned into acrylate esters, and the remaining is purified (98%-99.5% purity) into glacial acrylic acid (GAA). GAA is then used to make polyacrylic acid and modified into many products, such as superabsorbent polymers (SAPs), dispersants/antiscalants, or anionic polyelectrolytes for water treatment.
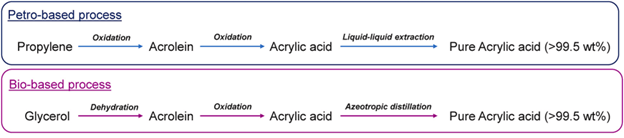
Other known bio-based processes also exist, where glycerol is dehydrated into acrolein, which is then oxidized to form acrylic acid. The proposed advantage of using glycerol is that it is a byproduct of biodiesel production, thus reducing dependencies on fossil fuels. However, bio-based processes' commercial viability and scalability are less mature than petro-based processes.
Given the technology readiness, solutions for reducing the carbon impact of acrylic acid via petro-based route are needed today. As such, research and development continues to thrive in both directions.
Regardless of the process, both routes utilize a raw material, propylene or glycerol, require steam and water, and emit wastegases, CO2, and wastewater. While each process undergoes numerous steps, both demand energy from heat sources to support chemical reactions and purification steps.
Heat Energy Requirements Between Acrylic Acid Production Routes
To produce acrylic acid, grant composite curves suggest that the cumulative heat generated from steam peaks at 488℃ and 505℃ for propylene and glycerol routes (Sadid et al., 2023). However, the heating and cooling equipment differ (see Table X), such as the need for more fired heaters for petro-routes, which burn fuel and can contribute to initial capital and operating costs. More fire heaters also maintain dependence on fossil fuels for acrylic acid production and contribute to CO2 emissions.
Research shows that a glycerol route generates about one-third less CO2 emissions than propylene, using a production basis of approximately 10,250 kg per hour of acrylic acid (Sadid etal., 2023). This amount is not a mere fraction and could translate into much lower CO2 taxes.
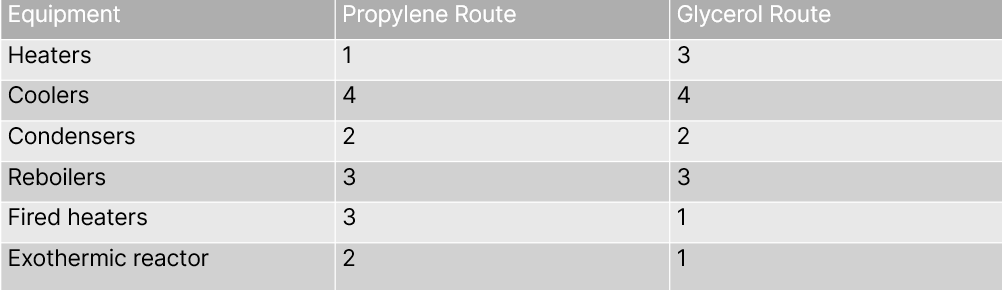
Additionally, a heat integration analysis shows slightly lower heating, but higher cooling energy savings can also be attained in the glycerol route. One point worth highlighting is that these estimates and comparisons are calculated without implementing alternative fuels, such as natural gas or renewable sources of heat energy, to generate steam or other forms of heat. Still, a detailed assessment indicates that glycerol routes would have lower capital expenditure and operating expenditure ($96.9 million and $224.4 million peryear, respectively) compared to the propylene route ($119.5 million and $235,9 million per year, respectively).
A central issue raised by the research team is that substantially more raw material for the bio-based route is needed to achieve comparable outputs of acrylic acid — approximately 100% more kg per hour of glycerol. The demand for so much complicates decision-making and clarity, and the finding necessitates a cradle-to-grave quantification of glycerol production itself. What is the impact of producing glycerol in such large quantities?
Environmental Impacts of Petro and Bio-based Acrylic Acid Routes
In a life cycle analysis, using a cradle-to-grave approach of acrylic acid, several environmental impacts consisting of (1) global warming, (2) water footprint, (3) acidification, (4) eutrophication, (5) ozone layer depletion, (6) photochemical smog, and (7) human toxicity, revealed the most significant environmental impacts for all purification processes were global warming, acidification, human toxicity, and water footprint (Bansod et al., 2024).
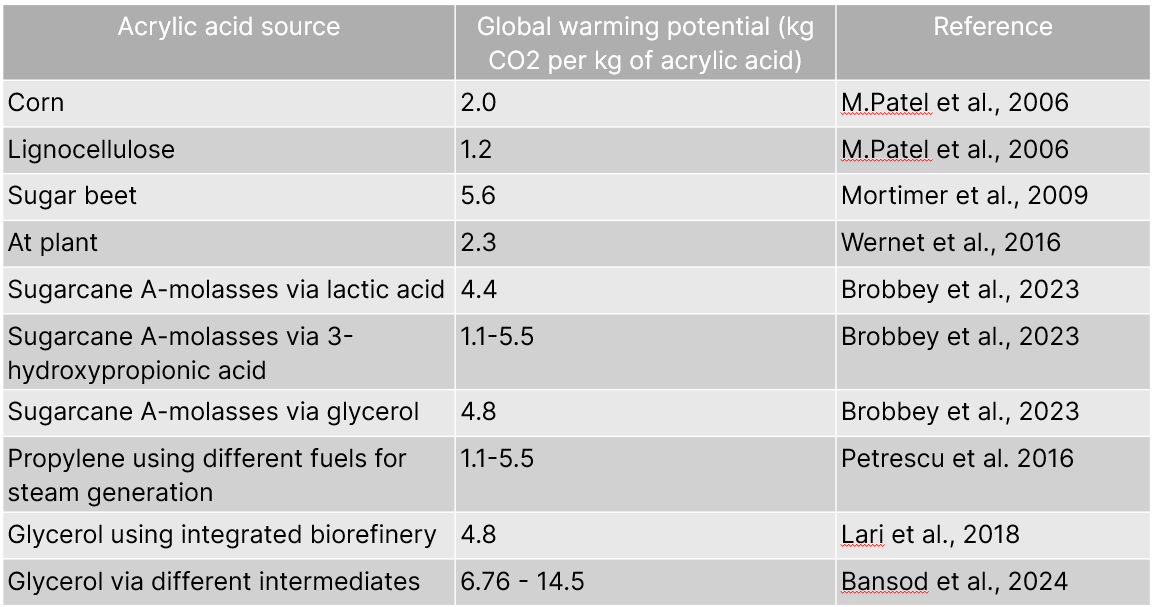
A most informative finding was that the raw materials for acrylic acid production were the main contributors to all seven impacts, followed by the production processes, whereas the storage and transport section had the minimum contribution (Bansod et al., 2024).
Generally, fossil-fuel-based pathways are considered unsustainable, and the cradle-to-grave approach for one of the latest life cycle analyses revealed that the propylene-based process has a lower GWP than glycerol-based processes (Bansod et al., 2024). Such findings should not, however, be a deterrent. The optimization of the glycerol-based process for producing acrylic ironically has a central challenge, which is an energy-intensive process requiring crude oil-based propylene and high-temperature reactions - which is unsustainable (Bagnato et al., 2017). Said differently, solutions like Kraftblock’s Net-Zero Heat System can help to improve the environmental impacts of petro-based acrylic acid routes by replacing fossil energy sources for preheating and steam generation with renewable electricity and a flexible, large-scale thermal energy storage.
This may also be applied at the initial steps for deriving glycerol, improving this route's carbon footprint. To understand that overlap, we must return to the propylene route.
Alternative fuels and energy sources for producing Acrylic Acid
In a life cycle analysis simulating 50,000 tonnes/year, researchers compared the environmental impacts of steam generation using different fuels for acrylic acid via the propylene route. Steam can be obtained using different fuels (e.g., natural gas, anthracite, lignite, heavy fuel oil, biomass, and a combination of natural gas and biomass).
The results showed that the worst case from an environmental point of view is when lignite is used for steam generation (Petrescu et al., 2016). The best case is generated by burning natural gas or biomass (Petrescu et al., 2016), but which is ultimately better is open to interpretation. Steam generation by natural gas leads to lower values for several other environmental impact indicators, such as Acidification Potential (AP); still, biomass gives the lowest value for Global Warming Potential (GWP).
Another consideration is the use of alternative sources to generate steam. Clean electricity with thermal energy storage would be an example of a viable replacement, which would, instead of burning natural gas or biomass fuels, would use the electricity from cheap times to supply process heat round-the-clock. Given the number of heaters, fired heaters, and reboilers known in the propylene route (refer to Table 1) and using data from the life cycle analysis (Petrescu et al., 2016), simulating 50,000 tonnes/year would massively mitigate sources of global warming alongside many other environmental impacts.
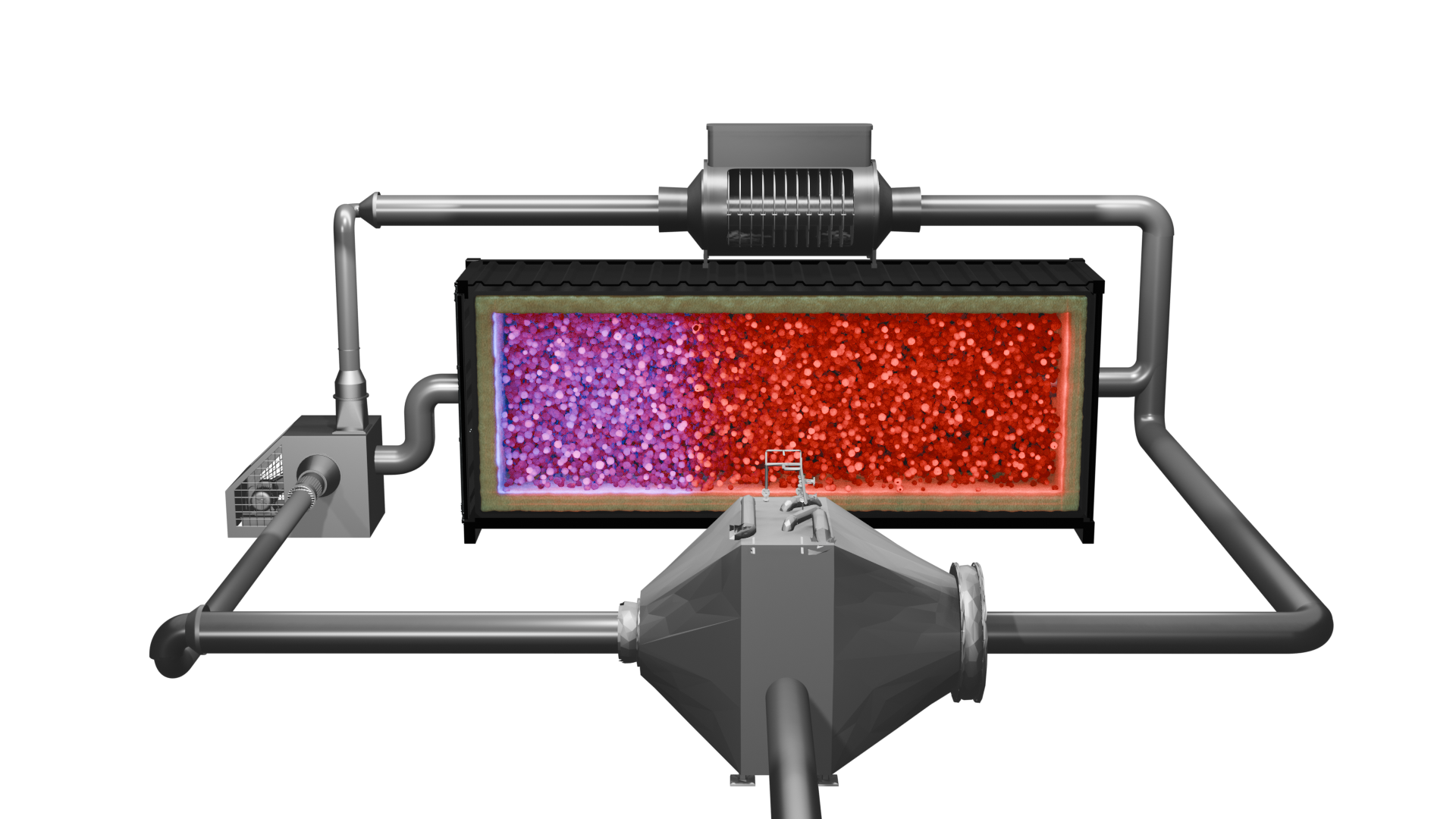
How much CO2 could be saved?
To put the effect into perspective, when coal or lignite is utilized as a fossil fuel to generate steam, the GWP hovers around 5525 kg CO2e/t and is reduced to 3877 kg CO2e/t for natural gas and 1095 kg CO2e/t for biomass fuels. Of course, additional economic and ecologic benefits are achieved by phasing out fossil fuels and replacing boilers and fired heaters with renewable electricity at their lowest cost — a transition made possible by Kraftblock’s Net-Zero Heat System.
References
Allied Market Research. (2022). Acrylic acidmarket size, share, growth forecast report, 2030. Allied Market Research. https://www.alliedmarketresearch.com/acrylic-acid-market S&P Global. (2023).
Acrylic acid and acrylate esters - Chemical economics handbook. S&P Global Commodity Insights.https://www.spglobal.com/commodityinsights/en/ci/products/acrylic-acid-acrylate-esters-chemical-economics-handbook.htmlDate of last access 03-10-2024
BASF, 2012 (last access 03-10-2024). http://product-finder.basf.com
Bagnato, G., Iulianelli, A., Sanna, A., & Basile, A. (2017). Glycerol Production and Transformation: A Critical Review with Particular Emphasis on Glycerol Reforming Reaction for Producing Hydrogen in Conventional and Membrane Reactors. Membranes,7(2).https://doi.org/10.3390/membranes7020017
Bansod, Y., Pawanipagar, P., Ghasemzadeh, K., & D'Agostino, C. (2024). Environmental sustainability evaluation of glycerol and propylene-based pathways to acrylic acid via differentintermediates. Green Chemistry. DOI: 10.1039/D4GC01329H
Petrescu, L., Fermeglia, M., & Cormos, C.(2016). Life Cycle Analysis applied to acrylic acid production process with different fuels for steam generation. Journal of Cleaner Production, 133,294-303. https://doi.org/10.1016/j.jclepro.2016.05.088
Sandid, A., Esteban, J., D'Agostino, C., &Spallina, V. (2023). Process assessment of renewable-based acrylic acid production from glycerol valorisation. Journal of Cleaner Production, 418,138127. https://doi.org/10.1016/j.jclepro.2023.138127